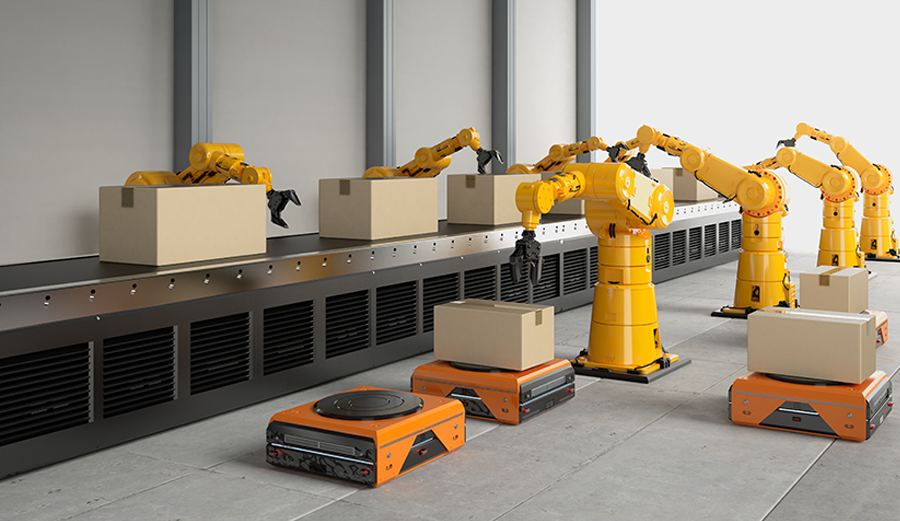
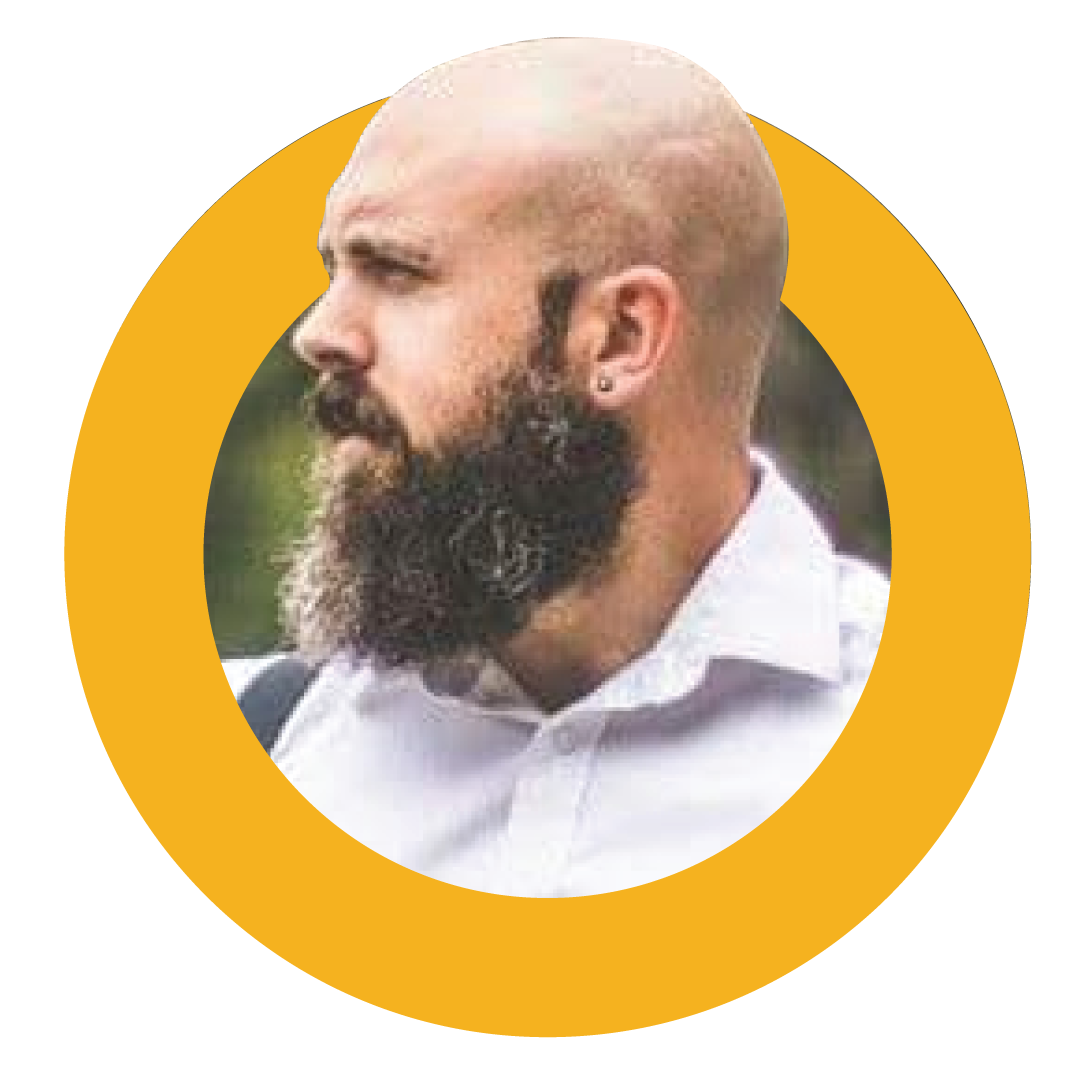
Caleb Connor, Manager, Supply Chain, Eclipse Automation
Beyond the Robot Arm: How End-to-End Automation Is Transforming Manufacturing
When we think of manufacturing automation, what often comes to mind is a robot arm assembling parts on a production line. It’s a powerful image—and an increasingly common sight in factories worldwide—but it represents just one small piece of the automation puzzle. As manufacturers continue to grapple with increasing competitive pressures and labor shortages, a more holistic approach to automation is emerging: one that spans the entire value chain from inbound logistics through production to warehousing and distribution.
This kind of comprehensive strategy isn’t really about replacing human workers with machines. It’s about thoughtfully automating less desirable, physically demanding, or difficult-to-staff positions in a way that creates an ecosystem that combines technology with humans to maximize value. And with 76% of supply chain and logistics leaders reporting notable workforce shortages—and 37% describing them as “high to extreme”—this strategy is graduating from a competitive advantage to an operational necessity.
In This Article
- End-to-end automation spans the entire manufacturing value chain, from inbound logistics to production to warehousing and distribution.
- Automated solutions like AGVs, AMRs, and collaborative robots help address labor shortages while improving safety and efficiency.
- Integrating automation technologies creates a seamless flow of materials and information, eliminating silos between operations.
- Strategic implementation focuses on highest-impact areas first, with each success funding future automation projects.
- The result is greater reliability, improved worker safety, and enhanced business efficiency in the face of persistent labor challenges.
From Loading Dock to Customer Doorstep
Consider the journey of a product through a fully automated manufacturing facility, starting with Automated Storage and Retrieval Systems (ASRS). This begins with automated guided vehicles (AGVs) or autonomous mobile robots (AMRs) unloading raw materials from delivery trucks and transporting them to storage. When needed, these same vehicles bring materials to the production line, where robots and cobots (collaborative robots) perform manufacturing functions alongside human workers who focus on skilled tasks that require judgment and dexterity.
Once finished, the products are picked up by robots, packaged, and transported to warehouse storage by AMRs that navigate freely without fixed pathways or human guidance. Throughout this process, digital systems track every movement and stat, creating a seamless flow of both materials and information.
“Automation and human + machine collaboration are digitally transforming manufacturing and optimizing supply chain operations to be more flexible, resilient, sustainable and safe,” says Nigel Stacey of Accenture Industry X.
Addressing Labor Challenges Across Functions
Taking an end-to-end approach means that labor challenges can be addressed throughout the value chain, not just on the production floor. Take retail, for example: supermarkets struggling to find reliable shelf-stocking staff can implement automated inventory management, warehouse management, and restocking systems. Distribution centers facing high turnover can deploy AMRs for order picking and implement data-driven supply chain optimization. Electronics manufacturers can use vision systems for quality control when skilled inspectors are scarce.
The benefits extend beyond merely filling positions. When DHL Supply Chain implemented Boston Dynamics’ Stretch robots to automate trailer unloading in its warehouses, it didn’t just replace human labor with an ASRS—it transformed operations. The robots, which take packages from the back of trailers and place them on conveyors, have achieved case unloading rates of up to 700 cases per hour, significantly exceeding manual methods. As Sally Miller, CIO of DHL Supply Chain North America notes, this automation addresses both safety concerns and labor challenges by “redirecting skilled labor to focus on value-add, strategic tasks in other areas of the warehouse.”
The Integration Advantage
The key to getting results like these is the integration between systems. When automation technologies communicate seamlessly, they eliminate the silos that typically separate manufacturing operations, inventory management, and logistics. The data generated creates visibility across the entire process, enabling better decision-making and responsiveness.
Consider a scenario where consumer demand triggers automatic adjustments throughout the value chain: AMRs reprioritize warehouse picking tasks, production schedules adjust in real-time, and AGVs reconfigure material delivery routes—all without manual intervention. This level of integration doesn’t just compensate for labor shortages; it creates new capabilities that wouldn’t be possible even with full staffing.
Starting the Journey
Implementing end-to-end automation isn’t an all-or-nothing proposition. The most successful manufacturers start with strategic automation of high-impact areas—often those with the most significant labor challenges or safety concerns, and those with the greatest anticipated impact on ROI—and gradually expand as each implementation proves its value.
For many companies, material handling offers the perfect starting point. Automating the transport of goods to and from production lines eliminates physically demanding work, improves safety by reducing heavy lifting, and creates immediate efficiency gains that can fund the next automation project.
As labor challenges persist across industries, manufacturers who take a holistic view of automation will gain a significant advantage. By implementing automated solutions throughout the value chain, companies can not only address staffing shortages but also create more reliable, safer, and efficient operations.
The future of manufacturing is partly about robots on assembly lines, but that’s just a small part of it. The real winners of the next phase of manufacturing automation improvements are the companies that create connected, intelligent systems that span the entire manufacturing ecosystem. Done properly, this approach increases reliability (where current supply chains are broken or unreliable), improves safety (by eliminating dangerous tasks), and drives the efficiency needed to compete in today’s challenging marketplace.
Curious to learn more about implementing end-to-end automation solutions for your manufacturing operations? Contact Eclipse Automation to explore how our industrial automation solutions can transform your entire value chain.

Get in touch to explore how our Advanced Engineering Services can help you move faster without compromising results.