
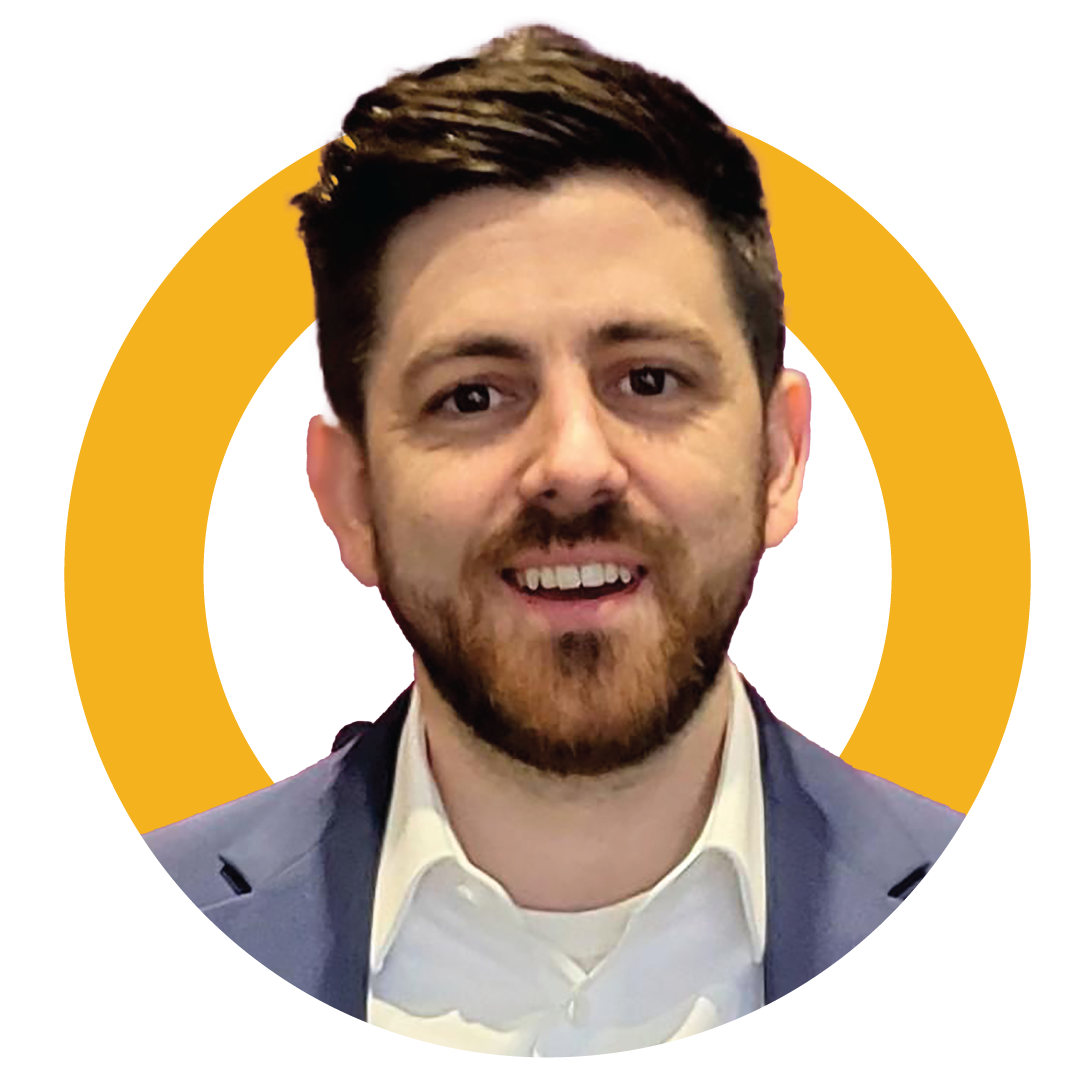
Brad Zalischuk, Engineer
Video gaming expertise is creating an unexpected talent pipeline for the future of manufacturing automation
When it comes to finding skilled workers for today’s high-tech manufacturing environment, traditional recruitment approaches often fall short. Reshoring manufacturing and creating new manufacturing jobs enjoys broad support in places like the US and Canada, but the reality is that many of those roles are increasingly hard to fill. With 85% of manufacturers reporting skilled worker shortages and a projected 2.1 million unfilled manufacturing positions by 2030, the industry faces an unprecedented talent crisis.
In response to global competition, manufacturers have been adapting with new technologies like Omniverse and digital twins, but to maximize their potential will take people who know how to use them. Currently, this skilled labor shortage is the biggest obstacle to improved productivity. But what if the solution is hiding in plain sight—in the bedrooms and living rooms where millions of video game devotees are developing complex digital and problem-solving skills on their own every day?
In This Article
- Gaming expertise offers manufacturers a ready supply of talent with transferable skills in 3D visualization, real-time decision making, and collaborative problem-solving.
- Manufacturers can leverage gaming talent to:
- Close the widening skills gap as experienced workers retire and traditional recruitment falls short
- Accelerate adaptation to emerging visualization technologies and interfaces
- Develop a workforce naturally aligned with emerging technologies like NVIDIA’s Omniverse platform
- Create new career pathways that didn’t exist before, and potentially recruit skilled workers from parallel industries to fill roles in highly technical areas like nuclear
Why gaming skills matter in modern manufacturing
Today’s manufacturing environment increasingly relies on digital technologies like 3D visualization, simulation, and interactive interfaces, which reduces time to market by improving planning and reducing change requests, among other things. The industry also relies increasingly on robot integration and programming to cut costs and fill roles that are hard to find humans for. All of these technologies share plenty of DNA with video games. As factories become more digital and automated, skills like navigating virtual spaces, adapting rapidly to new interfaces, and thinking strategically about systems are increasingly relevant.
Not only does video gaming potentially open up the talent pipeline for automation roles, it creates a workforce naturally attuned to the visualization, adaptability, and systems thinking required in modern manufacturing. As Brad Zalischuk, Program Manager of Digital Innovation and Transformation at Eclipse Automation explains, “I can see a future where an operations team running a manufacturing facility becomes more and more like playing an RTS (real-time strategy) game, like Starcraft or Factorio.”
Zalischuk, who describes himself as having been “obsessed with PCs” and “growing up on a desktop computer my whole life,” offers a clear example of how gaming experience can translate to the world of manufacturing innovation. His background has allowed him to recognize opportunities for using game engine technology in industrial applications that others missed—turning what would be “a painstaking process” into “one click button import, one click button view.”
This connection between gaming and industrial automation is creating a powerful opportunity for manufacturers willing to look beyond traditional recruitment channels.
A rare and valuable intersection of skills
The challenge for manufacturers is finding individuals who possess both gaming-related technical skills and manufacturing knowledge. As Zalischuk notes: “The tough thing right now is you’ll have people that have the gaming experience and they come from the game engine world—it’s a huge pool of people—but it’s very hard to find the people who have that sort of experience and have a deep understanding of custom automation and manufacturing.”
This intersection of skills can create a unique competitive advantage, though. “That overlap I think is extremely unique,” explains Zalischuk. Since developers and game developers likely have little familiarity with how automation and manufacturing work, manufacturers should recognize this overlap as a key to addressing workforce shortages, and continue to foster the development and application of new use cases.
Before the hire: Recognizing transferable skills from gaming
It’s one thing to review resumes looking for traditional manufacturing experience, and another to recognize valuable skills developed outside conventional career paths. Gamers develop capabilities directly applicable to modern manufacturing:
- 3D navigation fluency: As Zalischuk explains, “As we get to this world where our facilities are digitized, the machines are digitized… you need to be able to navigate a 3D stage quickly.” Gamers instinctively understand how to move through and interact with complex 3D environments, such as NVIDIA’s Omniverse platform.
- Interface adaptability: Gaming builds rapid adaptability. “Every time I start a new game I have to learn all the keybinds [gaming-specific keyboard shortcuts], how those controls work and adapt to that.” This adaptability is invaluable in manufacturing environments where software tools and interfaces constantly evolve.
- Systems thinking: Many kinds of digital games, from real-time strategy to open-world adventures, train players to understand complex, interconnected systems with multiple variables and dependencies, mirroring the complexity of modern automated manufacturing.
- Intrinsic motivation: Perhaps most valuable is the passion that gamers bring. Zalischuk describes the ideal fit for many of tomorrow’s digital factory roles as “that person that just really clicks and gets it and goes and downloads it on their home PC and plays with it… just messes around.” This intrinsic motivation—and the unquenchable sense of curiosity that underlies it—is one of the most reliable drivers of innovation.
- Technological fearlessness: Gamers are naturally comfortable exploring new technologies and pushing boundaries, creating a workforce that embraces rather than resists technological advancement.
In short, gaming builds a natural aptitude for the increasingly digital environment of modern smart factories, creating a ready supply of talent most manufacturers are completely overlooking.
Gaming skills in action: From onboarding to ongoing operations
When gaming talent enters the manufacturing environment, their impact extends from day one through long-term operations. Their gaming-developed capabilities translate into tangible business advantages:
- Accelerated learning curves: Every game brings with it a new interface, new rules, and new objectives, meaning that gamers are accustomed to tackling sometimes steep digital learning curves. Rather than viewing new technologies as intimidating, they’re more likely to approach them with a sense of interest and a problem-solving mindset.
- Strategic resource optimization: The resource management mindset from many strategy games doesn’t just help gamers understand manufacturing systems—it fundamentally changes how they operate them. Manufacturing operations and many RTS games both involve strategically allocating resources, anticipating bottlenecks, and continuously optimizing for efficiency.
- Fearless experimentation culture: Perhaps most valuable is how gaming backgrounds can reshape team dynamics, creating what one manufacturing supervisor called “a sandbox mentality” where controlled experiments are the norm rather than the exception. This balances continuous improvement with operational discipline, which can be difficult to achieve with traditionally trained staff.
The idea of tapping talent from outside domains with transferable skills is not new, of course. Nuclear engineering firm AtkinsRéalis, for example, recently began targeting workers in other industries after noting the overlap in capabilities. Building a gaming-to-manufacturing talent pipeline is very much in the same spirit, although perhaps a little less orthodox. It’s also a potentially powerful way for workers and employers to adapt to a shifting economy and compete for scarce talent, as employees seek out more stimulating, higher value opportunities.
But regardless of where they are first developed, recognizing transferable skills and creating career paths that leverage them are a key way that manufacturers can build more adaptable, technically fluent workforces. For an organization working to get ready for the challenges of Industry 4.0, the next great manufacturing automation hire may be honing their skills on a console right now.
Are you a gamer who pursued a path in manufacturing automation, or have you worked with someone whose gaming background gave them a leg up? We’d love to hear your experiences and perspective—please leave a comment below.
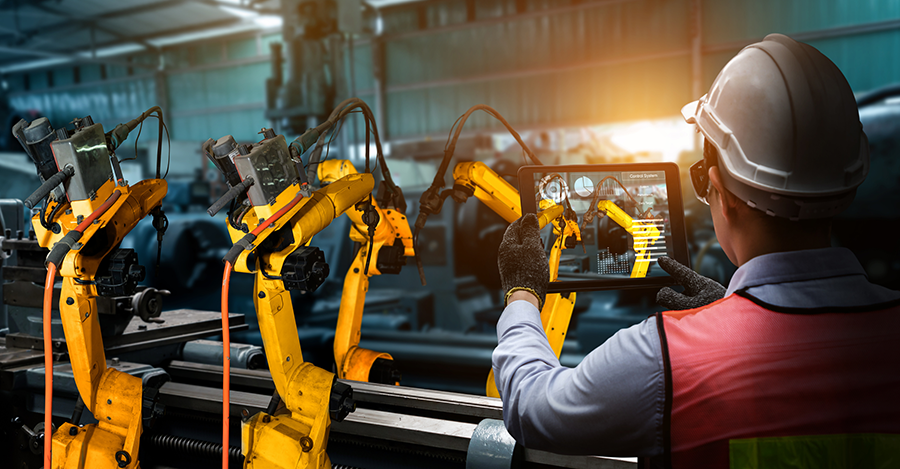
Get in touch to explore how our Advanced Engineering Services can help you move faster without compromising results.