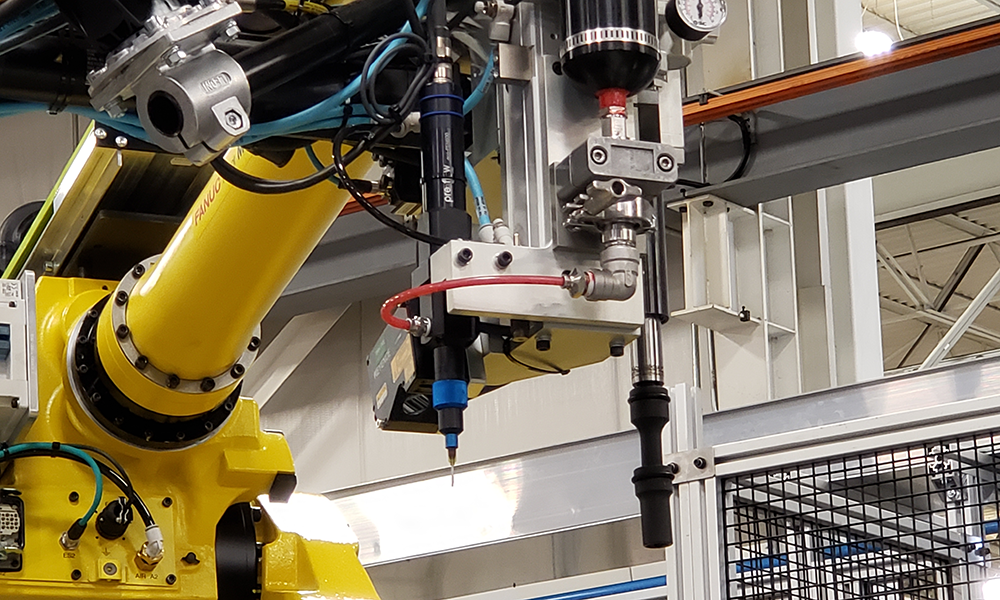
How automation prevents injuries
Of all the compelling reasons manufacturers have to move to automated systems, safety has got to rank high on that the list. Going from a manufacturing model that has workers doing manual assembly to one where operators are minding a machine that is doing the assembly comes with benefits that range from increased productivity, consistent quality, and a better bottom line. Automation makes manufacturing safer generally across the board, and for Eclipse Automation, a part of Accenture specifically, operator safety is a priority in the engineering of every one of the custom automated solutions they produce from start to finish.
Automation saves backs
It’s a fact that automation prevents common injuries. A manufacturing environment that has humans using vehicles and tools increases the risk of accidents. Think about just one action required of a worker: lifting. As their shift wears on, the worker may get weary, and this puts them at risk of fatigue-induced injuries. If the item they’re lifting is heavy or awkward, there is an even greater risk of a back injury. Manufacturers can take a load off by introducing a robot to do the heavy lifting, literally. Eclipse did just that when they engineered a system that builds prefab walls. The custom-built stud-handling system automates the process of inspecting, cutting to length, milling special features, marking the lumber, and assembling walls for residential and commercial construction. For operators, there is no lifting required, the risk is all but eliminated.
An automated system reduces risk of repetitive strain
Similarly, if it’s a worker’s job to tighten screws as part of the assembly process, they’re at risk of suffering from repetitive strain injury. But give a machine that task and the risk goes away, and along with it, the pain and suffering of the worker, the time lost both at work and at home, and for the manufacturer, all the associated costs of insurance claims and being short a worker. Eclipse designs, builds, and integrates automated systems in the life sciences sector that manufacture diagnostic devices. Assembly of these products requires working with tiny components and demands the utmost precision. With Eclipse’s system, robots perform the tasks over and over again with consistency and accuracy the way human operators cannot.
Automation goes where no person wants to go
Another way an automated system can keep workers safe goes beyond common injuries from contact with equipment or materials and relates more to the big picture of their entire work environment. Where conditions are hazardous, manufacturers can put systems in place to do whatever the required task is, and no human needs to be exposed to an unhealthy environment. Take for example, Eclipse Automation’s revolutionary, automated system for retrieving, sorting, and disposing of nuclear waste. They designed and built it so that an operator controls robot arms remotely, keeping the operator out of harm’s way.
Setting high standards for safe systems
Jules Topalian, Director of Engineering at Eclipse, says that operator safety is key to the design, build, and integration of every custom automated solution Eclipse produces. In fact, every system goes through rigorous tests to ensure it meets Eclipse’s own set of requirements, as well as regulatory requirements. A third-party auditing company, is consulted in both the design and build stages and ultimately certifies the machine for the jurisdiction it will be used in.
Built for operator safety and comfort
Certainly, every machine is designed with ergonomics in mind to prevent injuries, but Eclipse goes much further than this. In Jules’s words, their mission is to outpace the operator who could be tired or distracted and therefore vulnerable. For every design, the target operator they keep in mind is someone who is interested in the machine only and has no regard for safety. Human nature being what it is, engineers know that if there is a shortcut, some operators will often take it, but Eclipse engineers stay one step ahead. If, for example, there is an area on a machine that requires the operator to have both hands on it in order to keep it running, engineers design and build it so that the machine will not operate if an operator attempts to tie down one side in place of a hand or fashion any other sort of shortcut.
Safety reviews by a third party
Safety is a major component that is built right into every machine so that if the equipment fails, it fails in a safe manner. Eclipse designs equipment to monitor safety the whole time it’s running. After a machine is built, the team does a full review including scrutinizing the quality of the build to make sure there is no potential for injury, such as a gap where fingers could get pinched. Also, through a series of complicated calculations called stop-time calculations, and using sensors and controls, they determine how fast a machine can detect a person and stop itself to prevent injuring that person.
Exceeding standards
There are safety review meetings on all equipment at every stage from concept through to integration at the customer site. Plus, a third-party auditing company does a full review of everything from the drawings to the quality of the build. Every Eclipse machine is assessed for risk, and any risks identified are documented and given a risk category – either serious injury or slight injury. From there, the job is to mitigate the risk, whether it is a pinch point, cut point, crush hazard, or any other aspect that may expose an operator to injury. At the end, every machine meets or exceeds standards, including CSA, ISO, ANSI, and for equipment destined for the U.S., B11.
While manufacturers are embracing automation as a way to advance their businesses and become more productive and efficient, it is the job of the automation company to ensure that every one of the custom systems it designs and builds keep workers healthy and safe. Eclipse Automation is doing just that.
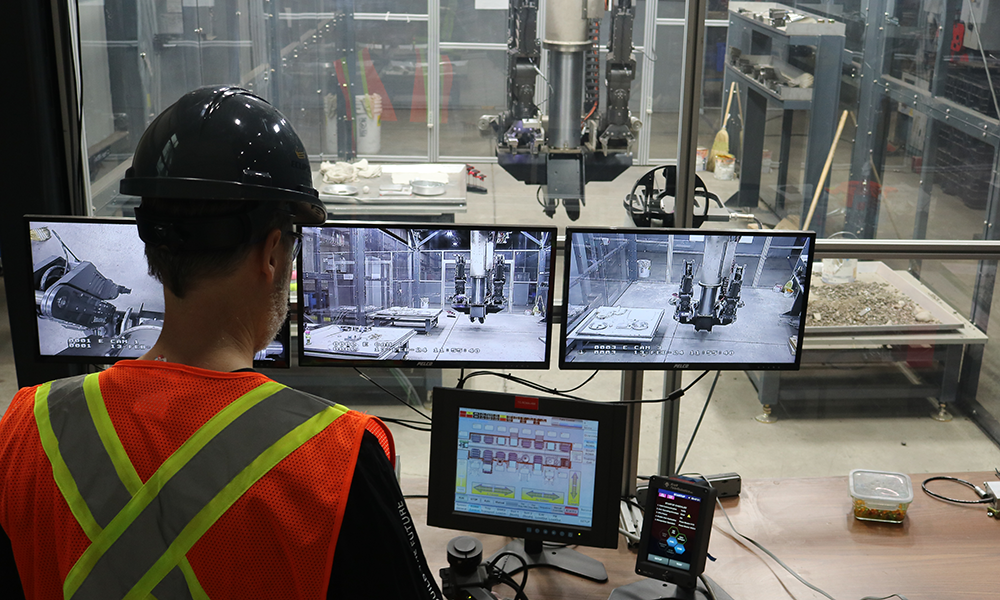