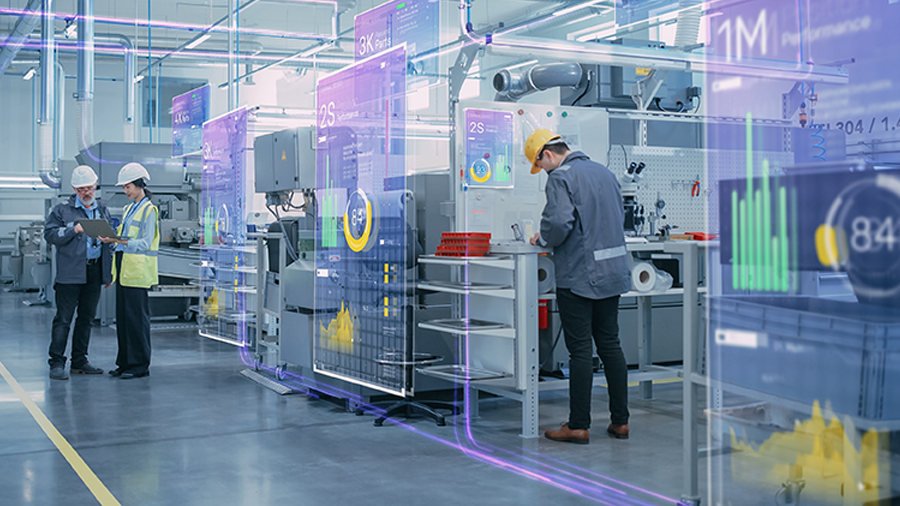
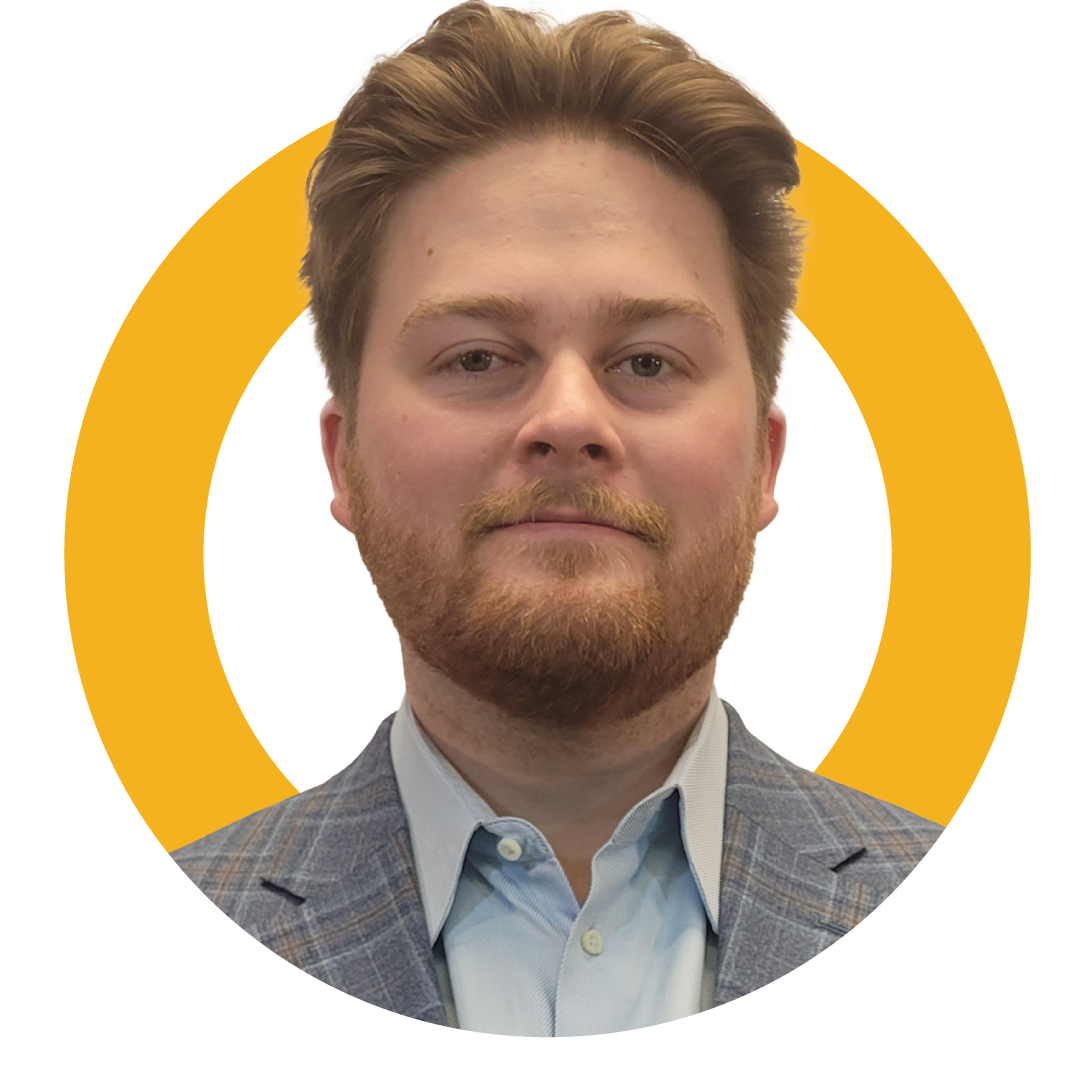
Ed Flood, Sales Manager
Streamlining Manufacturing Through Vertical Integration
As timelines shorten, standards lift, competition mounts, and new technologies proliferate, simply orchestrating all of the different elements involved in getting a new production line running can resemble four-dimensional chess. This is made doubly complex when—as is often the case—you’re working with multiple vendors. Communication gaps, schedule conflicts, inconsistent quality standards, and unpredictable integration issues can compromise timelines and performance objectives, wasting time and money, and putting the final outcome in jeopardy.
This is where vertical integration can make an enormous difference. Maintaining critical capabilities in-house (and being able to track them holistically) rather than distributing them across specialized providers can be a game-changer. By controlling the entire process from engineering design through fabrication, machining and build, an integrated organization can create a more cohesive execution model that reduces risk and time to market while improving outcomes.
In This Article
- Vertical integration in manufacturing automation encompasses engineering design, engineering construction, machining, fabrication, installation, and ongoing optimization.
- This unified approach eliminates coordination challenges and accountability gaps common in multi-vendor arrangements.
- The approach also benefits particularly complex projects where changing requirements and tight schedules create significant challenges.
- Eclipse Automation’s pandemic response demonstrates the real-world advantages of vertical integration in a time-critical situation.
Understanding Vertical Integration in Manufacturing
In manufacturing automation, vertical integration represents more than just a bunch of capabilities under one roof. It’s a different way of thinking, where everything from initial engineering design through precision machining, fabrication, electrical testing and commissioning, and ongoing support are in constant communication with each other, drastically reducing the cost of review and revision.
When automation projects involve multiple vendors, communication issues and handoff problems frequently create delays and quality risks. Every transition between companies introduces potential failure points. Vertical integration eliminates these transition points by bringing critical capabilities in-house.
This approach allows manufacturers to focus on their core business objectives while reducing the complexity of implementing advanced automation. Unlike distributed models that outsource critical functions, vertical integration maintains direct control over essential processes, which proves particularly valuable for complex manufacturing challenges with evolving requirements.
Essential Components of a Vertically Integrated Approach
An effective vertical integration model in manufacturing automation typically includes several key capabilities:
- Engineering Design: In-house engineering teams with experience developing solutions specifically tailored to manufacturing requirements, with direct responsibility for performance outcomes.
- Project Coordination: Centralized project leadership coordinating all aspects of the project, providing clear communication channels and ensuring alignment across all elements.
- Fabrication & Machining: Critical components produced within the same organization, ensuring precise specifications, consistent quality, full traceability, and reliable delivery…without third-party dependencies.
- Systems Integration: Consolidating the integration process to minimize interface challenges that typically emerge when multiple providers must synchronize their deliverables.
- Validation Protocols: Standardized testing that confirms system performance against each project’s unique needs and specifications before deployment.
- Ongoing Support: Continuous engagement throughout the system’s operational life to optimize performance and provide responsive maintenance.
Risk Mitigation Through Unified Responsibility
Even more than the time savings, arguably the biggest advantage of vertical integration is in how it reduces risk. By eliminating the multiple handoffs between separate vendors, an integrated approach addresses the most common failure points in complex automation initiatives:
- Knowledge Continuity: With multiple vendors, critical information often becomes fragmented or lost. An integrated team preserves technical knowledge across all disciplines.
- Schedule Management: In distributed approaches, delays from individual providers typically create cascading disruptions. An integrated model maintains consistent schedule control from concept through implementation.
- Clear Accountability: Multi-vendor arrangements often create confusion about responsibility when challenges arise. Vertical integration establishes clear ownership of performance across all system elements.
- Quality Standardization: Different suppliers typically operate with varying quality systems. An integrated methodology ensures uniform standards throughout each project phase.
Quality Standardization: Different suppliers typically operate with varying quality systems. An integrated methodology ensures uniform standards throughout each project phase.
Vertical Integration at Work: Eclipse Automation’s Pandemic Response
When the COVID-19 pandemic created critical shortages of N95 respirator masks in North America, Eclipse Automation demonstrated the practical advantages of vertical integration in a real-world crisis situation.
In April 2020, Eclipse formed a strategic partnership with Harmontronics Automation of China to bring N95 mask production capabilities to North America. Rather than simply importing equipment, Eclipse leveraged its vertically integrated capabilities—including engineering design and construction—to adapt the technology to North American standards and requirements.
According to Steve Mai, President and CEO of Eclipse Automation, the company’s comprehensive capabilities were essential to the rapid implementation: “Eclipse has the know-how to assess this system already producing N95 masks in China and see that any modifications required to meet North American specifications are done quickly and right.”
By maintaining control of the entire process, from initial design adaptation through installation and commissioning, Eclipse was able to begin production at our Cambridge, Ontario facility within just four weeks. In-house expertise in medical device manufacturing meant that from day one the system was able to meet strict North American standards. And we were able to quickly customize the system for specific manufacturer needs and support qualification efforts for various respirator designs.
The company eventually expanded capacity to produce approximately 130 million units of PPE annually, including 80 million respirators and 50 million surgical masks. This remarkable achievement would have been significantly more challenging without vertically integrated capabilities.
Evaluating the Long-Term Benefits
Implementing vertical integration requires real organizational commitment, to be sure. But it also delivers significant returns through accelerated project delivery, improved quality outcomes, and reduced implementation risk. For complex manufacturing automation challenges, it’s an approach that’s proven itself repeatedly.
When evaluating automation strategies, manufacturers should consider how vertical integration might address their specific challenges, particularly for projects where coordination complexity, timeline sensitivity, or quality requirements create significant risk factors.
Not every organization is set up for vertical integration, of course, and even organizations that would benefit from it do not necessarily need to vertically integrate every function—it depends on both the scope and goals of the project. The key is to identify which capabilities provide the greatest strategic value for your specific manufacturing challenges and build your integration strategy around those core competencies. If it’s time for your organization to consider this step, the right partner can make all the difference.
Interested in learning more about how a vertically integrated approach can improve your manufacturing automation outcomes? Contact Eclipse Automation to explore how our unique network and capabilities might benefit your next project.
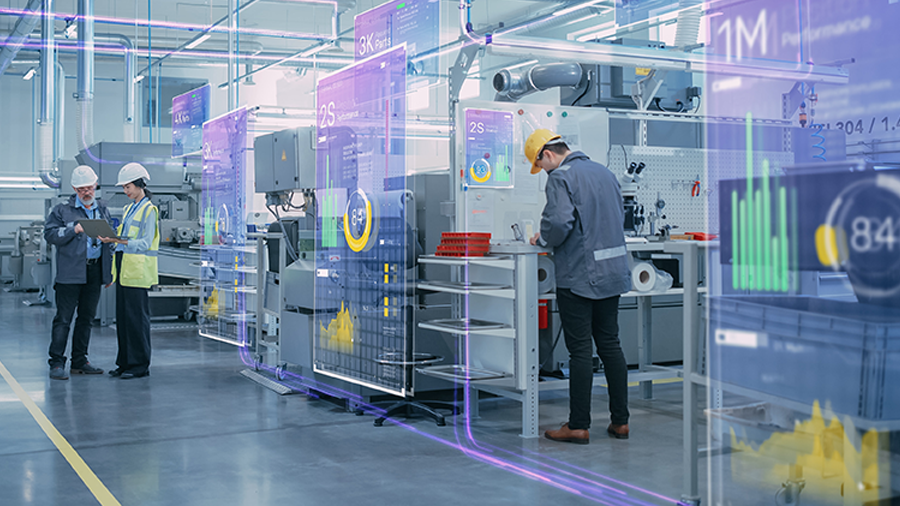
Get in touch to explore how our Advanced Engineering Services can help you move faster without compromising results.